RÜBIG
Maximaler Ofennutzraum: 1.200 x 900 x 900 mm (L x B x H)
Maximales Chargengewicht: 2.500 kg
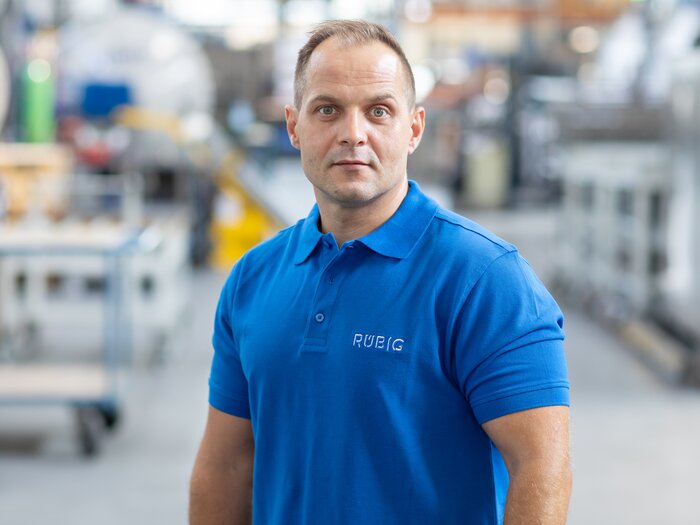
R.VAC+® repräsentiert die Gesamtheit der innovativen Vakuumhärteverfahren, die innerhalb der RÜBIG Härtetechnik angewandt werden.
Diese spezialisierten Verfahren zeichnen sich durch eine präzise Prozesskontrolle und einzigartige Qualitätsstandards aus, die eine konstante Härte, außergewöhnliche Zähigkeit und eine ideale Mikrostruktur der bearbeiteten Bauteile sicherstellen. Das Vakuumhärten, als Teil dieser hochentwickelten Technologiepalette, ist speziell für solche Bauteile konzipiert, die gegenüber Verformungen besonders empfindlich sind. Es findet Anwendung bei der Verarbeitung von Präzisionsteilen, komplex geformten Bauelementen und hochwertigen Werkzeugen, die nicht nur extremen Beanspruchungen standhalten müssen, sondern auch höchste Ansprüche an eine reine und glänzende Oberflächenbeschaffenheit erfüllen sollen.Dies ist besonders wichtig für Anwendungen, bei denen die ästhetische Erscheinung genauso kritisch ist wie die mechanische Leistungsfähigkeit. Durch die Anwendung der R.VAC+® Technologie in der RÜBIG Härtetechnik können Kunden somit von einer überlegenen Behandlungsqualität profitieren, die die Langlebigkeit und Zuverlässigkeit ihrer Komponenten unter verschiedensten Einsatzbedingungen garantiert.
R.VAC+® Verfahren im Überblick
Vakuumhärten
Vakuumhärten ist das Härteverfahren für verzugsempfindliche Präzisionsbauteile, Formteile und Werkzeuge mit hohen Anforderungen an eine saubere, blanke Oberfläche. Das Abschrecken erfolgt mit Gasstrom im Überdruck, der variiert werden kann, um die Abkühlungsbedingungen an die Bauteilanforderungen anzupassen. Die Werkstücke bleiben metallisch blank und zeigen keine Beeinflussung der Oberfläche (Verzunderung, Entkohlung), woraus ein niedrigerer Aufwand für die Hartbearbeitung gegenüber anderen Härteverfahren (z. B. Schutzgashärten) resultiert. Deshalb werden teure Einzel- und Serienwerkzeuge sowie hochwertige Formen und Bauteile im Vakuumofen wärmebehandelt.
Vorteile:
wenig Verzug
Metallisch blanke Oberflächen
Höhere Werkzeugstandzeiten
Präzise Dokumentation der komplizierten Prozessabläufe
Absolut reproduzierbare Behandlung
Helivac®
HELIVAC® stellt ein Sonderverfahren des Vakuumhärtens dar, welches bei höchsten Anforderungen an die Bauteileigenschaften Verwendung findet.
Durch die Verwendung von Helium anstelle von Stickstoff als Abschreckmedium resultieren folgende Vorteile:
Vorteile wie beim Vakuumhärten
minimaler Verzug
maximale Maßhaltigkeit
Udak
Die Unterdruckaufkohlung (auch Niederdruckaufkohlung) mit nachfolgender Gasabschreckung ist eine moderne Variante der Einsatzhärtung. Im Vergleich zur klassischen Gasaufkohlung mit Ölabschreckung kommen hier die Vorteile der Vakuumtechnik in Kombination mit der Gasabschreckung zu tragen:
- Verzugsarm
Keine Randoxidation
Auch für höher legierte Stähle geeignet (keine Passivierung)
Geeignete Werkstoffe:
Alle lufthärtenden Einsatzstähle (z.B. M50NiL, 300M, 18CrNiMo7-6, 18CrNi8)
Auch hochlegierte Stähle (z.B. X38CrMoV5-1)
Vorteile der Unterdruckaufkohlung:
Optimale Gleichmäßigkeit auch bei komplizierter Bauteilgeometrie und dichter Chargierung
Randoxidationsfreie Oberfläche
Saubere und blanke Oberfläche
Aufkohlung von hochlegierten, passivierenden Stählen
Vakuumlöten
Vakuumlöten bzw. Hochtemperaturlöten unter Vakuum ist ein thermisches Fügeverfahren, um Werkstoffe / Bauteilkomponenten fest und stoffschlüssig miteinander zu verbinden. Durch dieses Verfahren können komplexe Geometrien (z.B. komplizierte Kühlkanäle) bzw. mehrere Fügestellen / Nahtstellen in einem Prozess verbunden werden. Durch die hohe Temperatur in Kombination mit einem reduzierten Druckbereich (0,08 – 1 mbar) wird die werkstoffabhängige Oxidschicht thermisch aufgebrochen und ersetzt somit die Anwendung von Flussmittel.
Durch eine optimale Prozessführung und entsprechender Lote, können die Bauteile nicht nur fest und stoffschlüssig miteinander verbunden, sondern auch gleichzeitig gehärtet (Vakuumhärten) werden. Aus diesem Grund verwenden wir hauptsächlich eine Kupferbasis bzw. Nickelbasislote. Um optimale Lötverbindungen zu erzeugen, müssen entsprechende Spalte und Lotdepots bereits bei der Konstruktion berücksichtigt werden.
Lösungsglühen und Auslagern
Aushärten oder Auslagern (Anlassen) ist immer in Kombination mit einem vorhergehenden Lösungsglühen und Abschrecken zu verstehen. Durch diese Behandlung werden in Abhängigkeit von Material und Temperatur im Zeitverlauf feine Ausscheidungen (kohärent, teilkohärent oder inkohärent) in der Grundmatrix gebildet. Diese feinen Ausscheidungen (Phasen) behindern die Bewegungen von Versetzungen und steigern dadurch die Festigkeit.
Die Festigkeit/Härte und die mechanischen Eigenschaften werden durch die Auslagerungstemperatur bestimmt. Je nach Werkstoff (z.B. spezielle rostfreie Stähle, Maraginstähle, Titan, Aluminiumlegierungen, Bronzelegierungen) liegt die Auslagerungstemperatur (Anlasstemperatur) im Bereich von 150° C – 500° C.
Wie können wir unterstützen?
Wir beraten Sie sehr gerne persönlich. Kontaktieren Sie uns und erhalten Sie eine detailierte Auskunft über die von Ihnen gewünschte Behandlung!